Page 1 of 1
Making Acetal leadscrew nuts... DIY
Posted: Tue 08 May , 2012 9:25 am
by Denford Admin
This post is often referred to by Viceroy users wanting to get rid of backlash in their leadscrews. It will probably be a valid method for all smaller/hobbyist machines.
The author, Evan Williams has kindly given us permission to keep the information on this forum as well as the original site, which is here:
https://bbs.homeshopmachinist.net/showthread.php?t=43645
Re: Making Acetal leadscrew nuts... DIY
Posted: Tue 08 May , 2012 9:26 am
by Denford Admin

- lscrewnut1.jpg (163.13 KiB) Viewed 41727 times
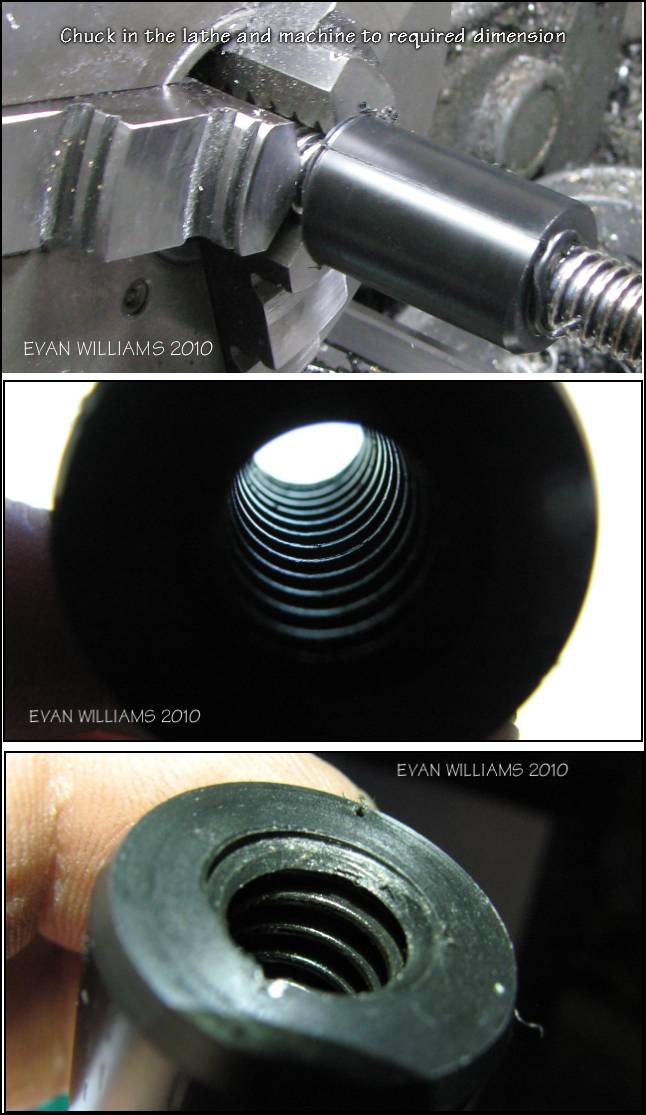
- lscrewnut2.jpg (75.19 KiB) Viewed 41727 times
The nut may be removed from the screw by chucking up the nut and and clamping the screw with vise grips, then turning it off in back gear. Use some oil on the screw and take it in small stages to avoid overheating the acetal from friction. After removal the nut may be chased out slightly by grinding a small slot on the end of the screw a couple of threads long. Put the nut in the fridge to shrink it a thou or two and then chase it with the screw while cold.
The nut and screw should be left to cool until both can be comfortably touched for a few seconds by bare hand. Then it may be water quenched the rest of the way to cold before attempting to remove the nut.
Re: Making Acetal leadscrew nuts... DIY
Posted: Tue 08 May , 2012 9:27 am
by Denford Admin
Chasing the nut if it's a bit too tight...
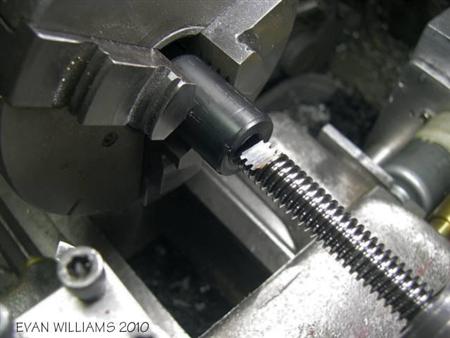
- lsnut.jpg (22.91 KiB) Viewed 41727 times
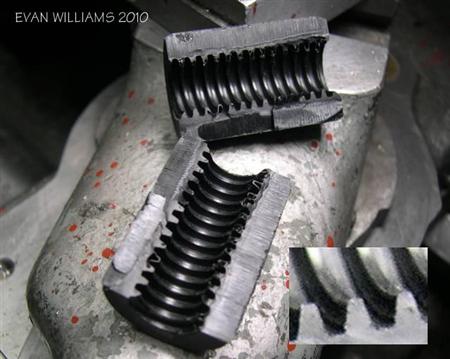
- lsnut1.jpg (27.51 KiB) Viewed 41727 times
I ground the screw to use it for chasing the threads like this:
This worked perfectly if you want it still slightly tight. Freezing or cooling it first should produce a perfect smooth fit. If you are using a screw that is from the machine then grinding just a small notch at one end should be sufficient although it will take more passes.
I then decided to crack it open to see what the threads look like. It took quite a bit of force to break it open. I wasn't expecting the threads to look this good.
Re: Making Acetal leadscrew nuts... DIY
Posted: Tue 08 May , 2012 9:28 am
by Denford Admin
FAQ:
In the picture where the leadscrew is chucked to the lathe, how do the two halves of the plastic hold together? Is it the heating that bonds the two?
--------------------------------------------------------------------------------
The melted acetal squeezes out into the kerf and heat welds the pieces together. I wouldn't depend on it in use so it would be a good idea to make a sleeve either from acetal or metal and press the nut into that.
This worked beautifully for me on the very first attempt so that tells me that it should be very easy to replicate.
What is the melting temp of acetal? Are we just going right up to the melting threshold with the heat?
--------------------------------------------------------------------------------
Short answers: 338F (170 Celsius), Yes.
Long answer: Acetal is limited to a maximum working temperature by the heat deflection temperature. This is load dependent. At a couple of hundred psi ( easily applied by the vise) the deflection temp is about 250F. This is when it begins to thermoform and consequently the amount of heat transmitted from the screw to the acetal increases as the contact area increases. As the temperature continues to rise the material softens further until liquidus is reached. This is easily observed as the acetal will quite suddenly start to flow. At that point the vise can be tightened some more and the acetal will squeeze out into the kerf and out the ends. It is important to heat mainly the screw as we don't want to melt the entire mass, only the inner portion.
Have you measured the backlash? I'm sure it's minimal but just wondering how much is there.
--------------------------------------------------------------------------------
There is zero backlash, nil, nada. It must be opened up slightly to make it easier to turn. As formed, it is difficult to turn by hand on the screw.
Are you making nuts for machine tools out of plastic???
--------------------------------------------------------------------------------
Acetal or Delrin is the material of choice for that application. If you can find a chunk at a reasonable price the only thing better is one of the PTFE filled varieties such as Torlon or Delrin AF or Ertalon and so forth. Plastic is the way to go as it is self wiping and doesn't wear the screw or itself. The Y axis nut on my mill is the original that I made from Acetal and it now has perhaps .0005 backlash. I made the shell for it in such a way that I can compress the nut and it removes any trace of backlash. I have made that adjustment only once.
My plastic Y axis nut hasn't even completely worn off the black oxide finish on the lead screw yet. It has hundreds of hours of running time on it. I purposely used bronze nuts and linear bearings on the X axis with plastic and PTFE on the Y axis so I could compare the long term wear and reliability. The Y axis is nearly pristine even though it is much more exposed to all the "grit" while the X axis shows significant wear both to the nuts and the lead screw as well as the linear bearings and rails. I will take some photos this evening when I have time. I will have to replace the bronze nuts, screw and the linear rails and shells fairly soon on the X axis. It will be with plastic nuts and bearings this time.
Acetal isn't the answer to everything as it has a limited static load capability. For the small home shop machine it is a winner. It is surprisingly stong and the impact resistance is superior to steel. Briggs and Stratton has been using acetal oil pump gears and acetal cams in their small engines for many years. Acetal gears are commonly used in the transmission of washing machines. I used acetal bushings to repair the 2" cast iron trunnion pegs on the yoke that drives the ram on my 16" shaper and they are holding up just fine.
Note: Don't try this techniques with the PTFE filled materials. The melting point is very different and if you overheat PTFE it will release toxic fumes. In this instance I didn't notice any trace of formaldehyde that might be released if the acetal is overheated. Be aware that it is a possibility and take measures to ventilate if needed. As long as the temperature is kept below about 500 degrees F this won't be an issue.
Re: Making Acetal leadscrew nuts... DIY
Posted: Fri 10 Aug , 2012 12:02 pm
by graham4877
Now thats a handy way to do it!