I've never got round to relating the tale of my lathe repair. It starts with a cautionary tale of using pallet couriers. To cut a long story short, somewhere between Scotland and home someone managed to (I assume) drop something on top of my newly acquired 280VS.
So some 'before' and 'after' pictures of what a courier can do to a machine.
to be continued...
Lathe rebuild
Moderators: Martin, Steve, Mr Magoo
-
- CNC Guru
- Posts: 396
- Joined: Mon 20 Nov , 2006 18:19 pm
- Hardware/Software: 280 VS lathe, Denford Senior E-type mill, Senior Major Universal Mill
- Location: East Midlands, UK
Lathe rebuild
- Attachments
-
- Before...
- My lathe front view.jpg (28.72 KiB) Viewed 9036 times
-
- After... tailstock
- tailstock end #1.jpg (17.24 KiB) Viewed 9036 times
-
- After...the chuck guard
- chuck guard #1.jpg (19.13 KiB) Viewed 9036 times
-
- After... the control panel
- Control Panel #1.jpg (11.08 KiB) Viewed 9036 times
-
- CNC Guru
- Posts: 396
- Joined: Mon 20 Nov , 2006 18:19 pm
- Hardware/Software: 280 VS lathe, Denford Senior E-type mill, Senior Major Universal Mill
- Location: East Midlands, UK
Re: Lathe rebuild
Amazingly, there didn't seem to be any damage to the bed, saddle, bearings, etc., so once I finally got a pay-out from their insurance it was time to see if it could be re-built.
A second similar machine (280VS with mechanical variable speed) became available and by good chance I found someone who was interested in it for other bits so we split the cost. This time it arrived safely - and I got various parts I needed, including useful tooling like a 4-jaw chuck and thread dial indicator. There were some exceptions that caught me out, like the rear splash-guard which was quite different in size and fitting, and the tailstock screw cap was also different.
So mechanically, it was just a case of hard graft to clean it all up (it was on it's back in the lorry when delivered, with oil everywhere!) and adjusting gibs, etc. Didn't need to touch the headstock bearings, but did have to take the headstock off, then re-seal and align it.
Electrically, it was a different story.
The circuit board was missing a few components and, being a bought-out item, Denford didn't have a schematic. No-one else that I could find had a board quite like mine, but through various web forums I eventually worked out the schematic, and all the components except the 7-segment displays are fairly easily available.
A second similar machine (280VS with mechanical variable speed) became available and by good chance I found someone who was interested in it for other bits so we split the cost. This time it arrived safely - and I got various parts I needed, including useful tooling like a 4-jaw chuck and thread dial indicator. There were some exceptions that caught me out, like the rear splash-guard which was quite different in size and fitting, and the tailstock screw cap was also different.
So mechanically, it was just a case of hard graft to clean it all up (it was on it's back in the lorry when delivered, with oil everywhere!) and adjusting gibs, etc. Didn't need to touch the headstock bearings, but did have to take the headstock off, then re-seal and align it.
Electrically, it was a different story.
The circuit board was missing a few components and, being a bought-out item, Denford didn't have a schematic. No-one else that I could find had a board quite like mine, but through various web forums I eventually worked out the schematic, and all the components except the 7-segment displays are fairly easily available.
- Attachments
-
- Damaged circuit board
- circuit board side#1.jpg (9.85 KiB) Viewed 9035 times
-
- CNC Guru
- Posts: 396
- Joined: Mon 20 Nov , 2006 18:19 pm
- Hardware/Software: 280 VS lathe, Denford Senior E-type mill, Senior Major Universal Mill
- Location: East Midlands, UK
Re: Lathe rebuild
A new box for the control panel was 'found' at work. Being a different shape, the original fascia plate wouldn't fit, and was pretty tatty after being flattened out. So I measured it up and re-drew all the graphics which were printed onto a self-adhesive film and stuck onto my newly made front plate.
A new mount for the control box was fabricated, then came the fun of wiring it all up - many wires had lost their markings so they all had to be traced back to the contactor board.
Finally it was all done and power applied from my home-built 3-phase converter. This was when I found out that these machines need 415V 3-ph - although the spindle and suds pump motors can be re-wired for 240V, the cut-outs can't be adjusted for the extra current and the vari-speed motor needs 415V or did doesn't have enough power to shift the Simplabelt pulley.
The 'tin work' was sorted by judicious use of a large hammer, big bits of wood and 6" G-clamps. There are a couple of dents still visible, but it all fits now and only gets covered in swarf anyway. Lathes aren't there to look pretty, are they?
A new mount for the control box was fabricated, then came the fun of wiring it all up - many wires had lost their markings so they all had to be traced back to the contactor board.
Finally it was all done and power applied from my home-built 3-phase converter. This was when I found out that these machines need 415V 3-ph - although the spindle and suds pump motors can be re-wired for 240V, the cut-outs can't be adjusted for the extra current and the vari-speed motor needs 415V or did doesn't have enough power to shift the Simplabelt pulley.
The 'tin work' was sorted by judicious use of a large hammer, big bits of wood and 6" G-clamps. There are a couple of dents still visible, but it all fits now and only gets covered in swarf anyway. Lathes aren't there to look pretty, are they?
- Denford Admin
- Site Admin
- Posts: 3649
- Joined: Fri 10 Feb , 2006 12:40 pm
- Hardware/Software: Go to User Control Panel > Profile
Enter as much information about your CNC hardware and software as you can - it makes it easier for everyone to know what you're talking about then. - Location: Sunny Brighouse
- Contact:
Re: Lathe rebuild
Thanks Andy - its great to be able to see the reasons behind all the information requests we get - it makes it more worthwhile.
Sorry but I couldn't help but laugh at the state of the control box - what were they thinking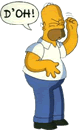
Sorry but I couldn't help but laugh at the state of the control box - what were they thinking
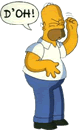
-
- CNC Guru
- Posts: 396
- Joined: Mon 20 Nov , 2006 18:19 pm
- Hardware/Software: 280 VS lathe, Denford Senior E-type mill, Senior Major Universal Mill
- Location: East Midlands, UK
Re: Lathe rebuild
My new control box.
Yes, I can laugh at the state of the old one now too!
Yes, I can laugh at the state of the old one now too!
- Attachments
-
- New control box in place. Everything cleaned-up, headstock cover plate fixed back on properly (all 4 screws had been sheared through), and replacement chuck-guard fitted.
- Headstock & Control box #.jpg (21.9 KiB) Viewed 9015 times
-
- New panel compared to the old, flattened-out, front plate.
- New & old control panels#.jpg (24.49 KiB) Viewed 9015 times