MIRAC UPDATING TO MASSO G3
Moderators: Martin, Steve, Mr Magoo
MIRAC UPDATING TO MASSO G3
hello everyone hope to get some help i am upgrading my denford mirac lathe marked in 1997 i chose MASOO G3 for my upgrade so i am having trouble with my ATC i chose 4BITS tool changer could you please guide me if i chose changer Right? Well regardless of whether I chose well this is what is happening, the turret makes the changes only that the 4-bit codes do not seem to be correct and the binary numbers do not match, I made a list of the LEDs that turn on every time I select a tool , I will leave some photos of my list and of the turret that I have also there is a gyro encoder behind the turret.
- Attachments
-
- IMG_20210310_201226.jpg (213.69 KiB) Viewed 13620 times
-
- IMG_20190929_201422.jpg (154.07 KiB) Viewed 13620 times
-
- IMG_20210309_181817.jpg (540.57 KiB) Viewed 13620 times
-
- IMG_20210412_210358.jpg (136.4 KiB) Viewed 13620 times
- Iron-Man
- CNC Apprentice
- Posts: 81
- Joined: Mon 28 Feb , 2011 9:40 am
- Hardware/Software: Modified NovaTurn with Yaskawa AC Servos +-10V, PathPilot running on a GizmoSphere 1 with Ibob2 PCIE interface that I designed. Denford Triac to be modified with AC Servos.
Re: MIRAC UPDATING TO MASSO G3
Hello Mendez !
Did you ever solve your turret problem?
Iron-Man
Did you ever solve your turret problem?
Iron-Man
Re: MIRAC UPDATING TO MASSO G3
Hello man, not yet, the problem is still valid and there is a disadvantage with MASSO that you cannot access the macros to be able to edit, by the way I have seen the great job you did with your novaturn, I also have one even though I don't I have launched.
- Iron-Man
- CNC Apprentice
- Posts: 81
- Joined: Mon 28 Feb , 2011 9:40 am
- Hardware/Software: Modified NovaTurn with Yaskawa AC Servos +-10V, PathPilot running on a GizmoSphere 1 with Ibob2 PCIE interface that I designed. Denford Triac to be modified with AC Servos.
Re: MIRAC UPDATING TO MASSO G3
Have you double checked the absolute encoder for errors? If you can get it to index and lock, this is a good thing. Do you need to convert the logic to get correct tool number?
Also, which version of the turret do you have?
Iron-Man
Also, which version of the turret do you have?
Iron-Man
Re: MIRAC UPDATING TO MASSO G3
hello iron man, sorry for taking time to respond, my turret is a DM8 these turrets do not have an encoder for each position, instead they have a rotary selector with 8 signals that go out and go to a diode module, I leave you a photo .![Image]()
- Attachments
-
- IMG_20210325_125302.jpg (332.96 KiB) Viewed 13084 times
- Iron-Man
- CNC Apprentice
- Posts: 81
- Joined: Mon 28 Feb , 2011 9:40 am
- Hardware/Software: Modified NovaTurn with Yaskawa AC Servos +-10V, PathPilot running on a GizmoSphere 1 with Ibob2 PCIE interface that I designed. Denford Triac to be modified with AC Servos.
Re: MIRAC UPDATING TO MASSO G3
Can you read the part number on the Grayhill 8 position switch?
Iron-Man
Iron-Man
Re: MIRAC UPDATING TO MASSO G3
yes, the model is 44A45-01-1-08N
- Iron-Man
- CNC Apprentice
- Posts: 81
- Joined: Mon 28 Feb , 2011 9:40 am
- Hardware/Software: Modified NovaTurn with Yaskawa AC Servos +-10V, PathPilot running on a GizmoSphere 1 with Ibob2 PCIE interface that I designed. Denford Triac to be modified with AC Servos.
Re: MIRAC UPDATING TO MASSO G3
I have looked at this a little closer. I think you should try the EMCOturn 120 turret. If you look at the page it shows the exact logic you will need to get the correct functioning of the turret. Now the main problem, I do not think that you can get the correct logic function from the Grayhill switch. It appears to be just a simple switch, no BCD, Gray code etc. Do you have the diode schematic?
From MASSO: EMCOturn 120
Input Signal Sequence Chart
Wire the sensor inputs and assign to MASSO as below:
Tool Changer - Input 1 for Turret signal-1
Tool Changer - Input 2 for Turret signal-2
Tool Changer - Input 3 for Turret signal-3
Tool Changer - Input 4 for Turret signal-4
Input Signal Sequence Chart
The below chart shows the signal sequence as per EMCO documentation. Check that your tool turret provides the signals as shown below to work properly with MASSO.
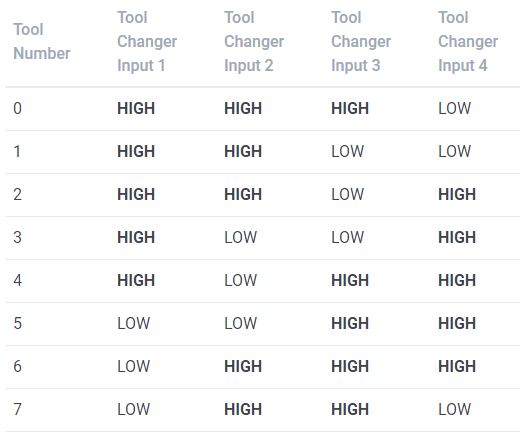
I can check and see if there are any 8 bit to 4 bit converter logic ICs or Priority Encoder ICs available. If not, you could use a pic micro and simply write the software for a conversion. Something like this:
// Endless loop
IF TOOL 0 TRUE, ie Grayhill (0) HIGH, THEN OUTPUT A = HIGH, OUTPUT B = HIGH, OUTPUT C= HIGH, OUTPUT D =LOW
IF TOOL 1 TRUE, ie Grayhill (1) HIGH, THEN OUTPUT A = HIGH, OUTPUT B = HIGH, OUTPUT C= LOW, OUTPUT D =LOW
IF TOOL 2 TRUE
.
.
.
IF TOOL 7 TRUE, ie Grayhill (7) HIGH, THEN OUTPUT A = LOW, OUTPUT B = HIGH, OUTPUT C= HIGH, OUTPUT D =LOW
// Loop forever
You could name these anything. Using a PIC would allow you to make changes in the future. You would need 8 inputs, 4 outputs.
Hope this helps,
Iron-Man
From MASSO: EMCOturn 120
Input Signal Sequence Chart
Wire the sensor inputs and assign to MASSO as below:
Tool Changer - Input 1 for Turret signal-1
Tool Changer - Input 2 for Turret signal-2
Tool Changer - Input 3 for Turret signal-3
Tool Changer - Input 4 for Turret signal-4
Input Signal Sequence Chart
The below chart shows the signal sequence as per EMCO documentation. Check that your tool turret provides the signals as shown below to work properly with MASSO.
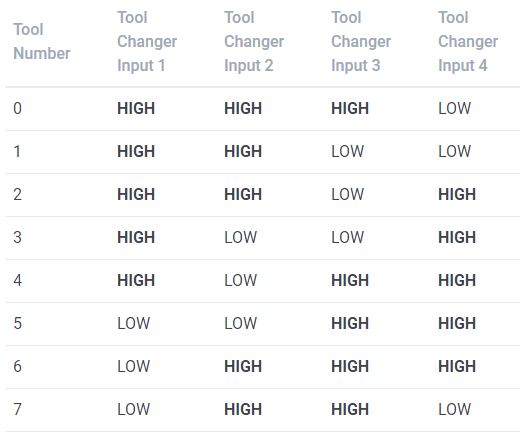
I can check and see if there are any 8 bit to 4 bit converter logic ICs or Priority Encoder ICs available. If not, you could use a pic micro and simply write the software for a conversion. Something like this:
// Endless loop
IF TOOL 0 TRUE, ie Grayhill (0) HIGH, THEN OUTPUT A = HIGH, OUTPUT B = HIGH, OUTPUT C= HIGH, OUTPUT D =LOW
IF TOOL 1 TRUE, ie Grayhill (1) HIGH, THEN OUTPUT A = HIGH, OUTPUT B = HIGH, OUTPUT C= LOW, OUTPUT D =LOW
IF TOOL 2 TRUE
.
.
.
IF TOOL 7 TRUE, ie Grayhill (7) HIGH, THEN OUTPUT A = LOW, OUTPUT B = HIGH, OUTPUT C= HIGH, OUTPUT D =LOW
// Loop forever
You could name these anything. Using a PIC would allow you to make changes in the future. You would need 8 inputs, 4 outputs.
Hope this helps,
Iron-Man
Re: MIRAC UPDATING TO MASSO G3
Hello, thanks for answering, I will leave a pdf file of the diode modules and the signals that come out of the turret, I also sent an email to MASSO and this is what they told me:
It seems the problem is being caused by relay timing because relays are mechanical devices and will have small time delays (milliseconds) and this will have a huge impact on logic and in fact with relays it will never work reliably . Also, it is not necessary to have relays in this type of configuration.
.
Can you connect the diode signals to MASSO directly? We hope this removes the timing issue and your tool changer works fine. do this test and keep using MASSO 4 bit tool logic as it is the best choice for your setup let us know how it goes.
It seems the problem is being caused by relay timing because relays are mechanical devices and will have small time delays (milliseconds) and this will have a huge impact on logic and in fact with relays it will never work reliably . Also, it is not necessary to have relays in this type of configuration.
.
Can you connect the diode signals to MASSO directly? We hope this removes the timing issue and your tool changer works fine. do this test and keep using MASSO 4 bit tool logic as it is the best choice for your setup let us know how it goes.
- Attachments
-
- AC3R-10A.pdf
- (47.38 KiB) Downloaded 511 times
-
- AC3R-09A.pdf
- (71.32 KiB) Downloaded 492 times